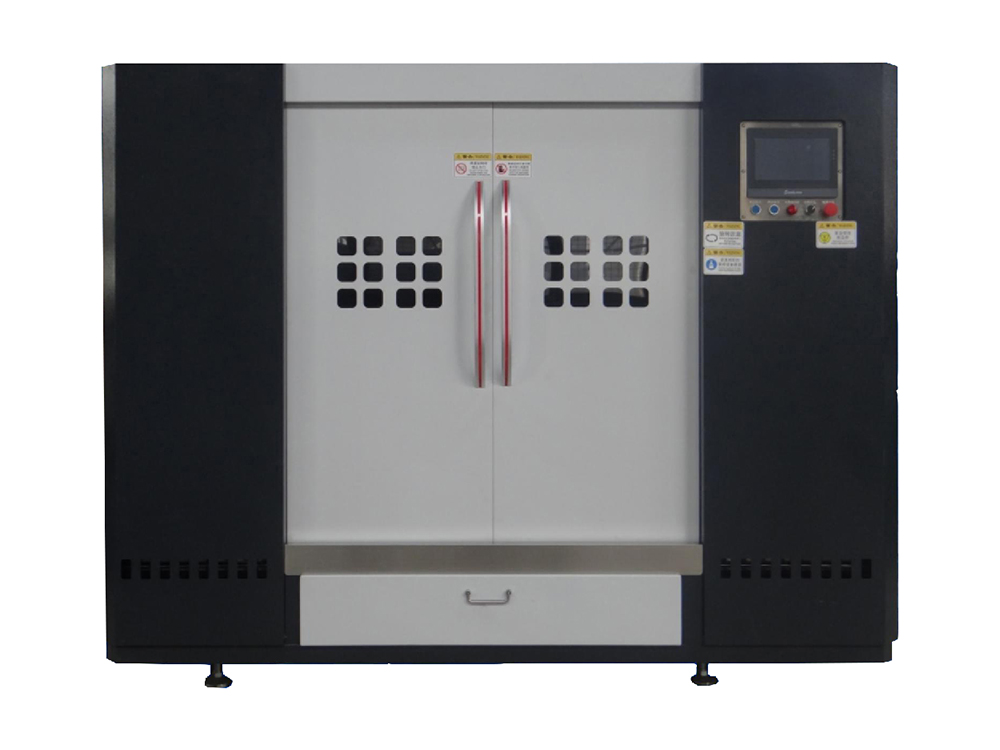
# Dry Polishing Machine for Efficient Surface Finishing
## Introduction to Dry Polishing Machines
Dry polishing machines have revolutionized the surface finishing industry by offering a dust-free and efficient alternative to traditional wet polishing methods. These machines utilize advanced technology to achieve high-quality finishes without the need for water or other liquids, making them environmentally friendly and cost-effective.
## How Dry Polishing Machines Work
Unlike conventional polishing systems, dry polishing machines employ specialized abrasives and polishing pads that generate minimal heat and dust. The process involves:
– Using diamond-impregnated polishing tools
– Incorporating dust extraction systems
– Applying controlled pressure for optimal results
– Achieving consistent finishes across various materials
## Benefits of Dry Polishing Technology
The adoption of dry polishing machines offers numerous advantages for industrial and commercial applications:
### Environmental Advantages
Dry polishing eliminates water consumption and prevents slurry waste, significantly reducing environmental impact. The integrated dust collection systems ensure cleaner work environments and better air quality.
### Cost Efficiency
By removing water from the polishing process, businesses can save on:
– Water consumption costs
– Waste disposal expenses
– Maintenance requirements
– Downtime associated with wet processes
### Improved Productivity
These machines typically offer:
– Faster polishing cycles
– Consistent results
– Reduced cleanup time
– Continuous operation capabilities
## Applications Across Industries
Dry polishing machines serve diverse sectors with their versatile performance:
### Construction and Flooring
Ideal for concrete, terrazzo, and stone floor finishing, these machines provide high-gloss surfaces without water damage or staining risks.
### Metal Fabrication
Used for polishing stainless steel, aluminum, and other metals, dry systems prevent water spotting and corrosion issues.
### Automotive and Aerospace
Critical for finishing components where moisture contamination must be avoided, ensuring precision and quality in sensitive applications.
## Choosing the Right Dry Polishing Machine
When selecting a dry polishing system, consider these factors:
– Material type and hardness
– Desired finish quality
Keyword: dry polishing machine
– Production volume requirements
– Available power sources
– Dust extraction efficiency
– Machine weight and maneuverability
## Maintenance and Care
Proper maintenance ensures optimal performance and longevity:
– Regularly clean dust collection systems
– Inspect and replace polishing tools as needed
– Check electrical components periodically
– Lubricate moving parts according to manufacturer guidelines
– Store in clean, dry environments
## Future Trends in Dry Polishing
The industry continues to evolve with:
– Smart polishing systems with automated controls
– Improved dust extraction technologies
– Advanced abrasive materials
– Energy-efficient designs
– Integration with Industry 4.0 systems
## Conclusion
Dry polishing machines represent a significant advancement in surface finishing technology, offering businesses an efficient, eco-friendly, and cost-effective solution. As industries continue to prioritize sustainability and productivity, these systems are becoming essential tools for achieving superior finishes across various materials and applications.