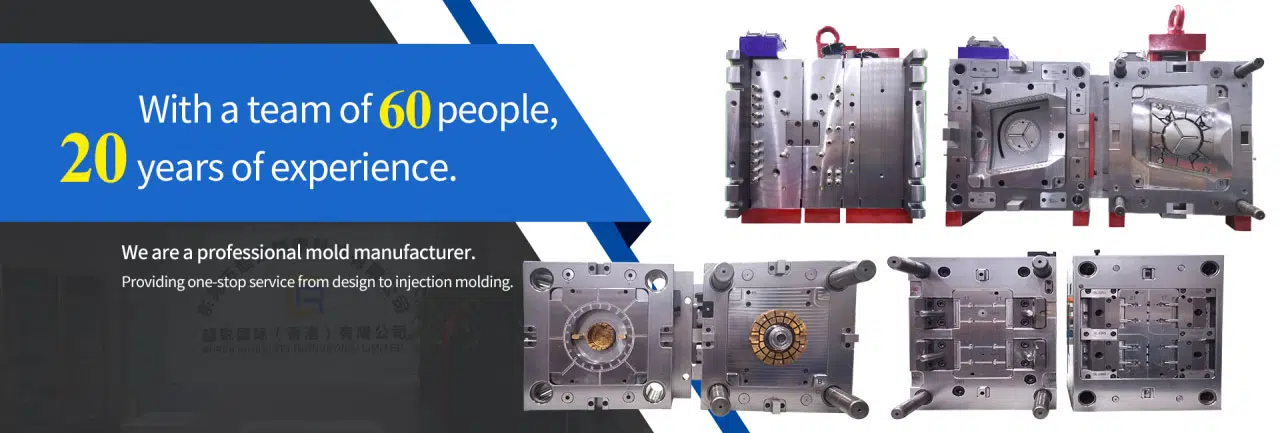
# Vacuum Casting Process in Manufacturing
## Introduction to Vacuum Casting
Vacuum casting is a versatile manufacturing process widely used for producing high-quality prototypes and small-batch production parts. This technique combines the benefits of traditional casting with modern vacuum technology to create precise and detailed components.
## How Vacuum Casting Works
The vacuum casting process involves several key steps:
### 1. Master Pattern Creation
A master pattern is first created using CNC machining or 3D printing. This pattern serves as the original model for the casting process.
### 2. Silicone Mold Making
The master pattern is placed in a casting box, and liquid silicone is poured around it. The entire assembly is then placed in a vacuum chamber to remove air bubbles before curing.
### 3. Casting Process
Once the silicone mold is ready, polyurethane resin is poured into the mold cavity while under vacuum. The vacuum ensures complete filling of all mold details and eliminates air pockets.
### 4. Curing and Demolding
Keyword: Vacuum Casting
The cast part is allowed to cure, typically at elevated temperatures, before being carefully removed from the silicone mold.
## Advantages of Vacuum Casting
Vacuum casting offers numerous benefits for manufacturers:
– High accuracy and fine detail reproduction
– Ability to produce parts with complex geometries
– Cost-effective for small production runs
– Wide range of material options with different properties
– Fast turnaround times compared to traditional manufacturing methods
– Excellent surface finish quality
## Applications of Vacuum Casting
This manufacturing process finds applications across various industries:
### Automotive Industry
Used for creating functional prototypes of interior components, housings, and under-the-hood parts.
### Medical Devices
Ideal for producing small batches of medical equipment prototypes with precise requirements.
### Consumer Electronics
Commonly employed for creating housing prototypes and functional testing models.
### Aerospace Components
Used for manufacturing lightweight, high-strength parts for testing and validation.
## Material Options in Vacuum Casting
Vacuum casting supports a wide variety of polyurethane resins that can mimic different engineering plastics:
– ABS-like materials
– PP-like materials
– PC-like materials
– Rubber-like materials
– Transparent materials
– High-temperature resistant materials
## Quality Control in Vacuum Casting
To ensure consistent quality, manufacturers implement several quality control measures:
– Visual inspection of all cast parts
– Dimensional verification using CMM or other measuring tools
– Material property testing
– Surface finish evaluation
– Functional testing where applicable
## Future Trends in Vacuum Casting Technology
The vacuum casting industry continues to evolve with several emerging trends:
– Development of new resin materials with enhanced properties
– Integration with digital manufacturing technologies
– Improved automation in the casting process
– Enhanced sustainability through material recycling
– Combination with other rapid manufacturing techniques
Vacuum casting remains a valuable manufacturing process that bridges the gap between prototyping and mass production, offering manufacturers flexibility, speed, and cost-efficiency for low to medium volume production needs.