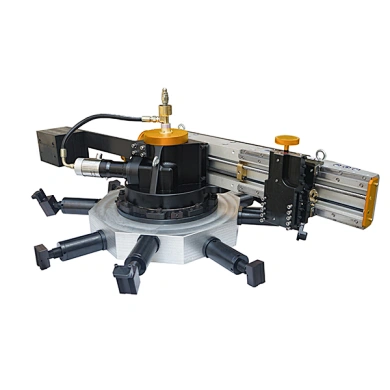
,字数要求2000字以上
html
Chemical Plant Flange Preparation Machine for Maintenance
In the demanding environment of chemical plants, maintaining equipment integrity is crucial for operational safety and efficiency. One critical aspect of this maintenance involves flange preparation – a process that ensures proper sealing and connection between piping systems. The Flange Preparation Machine for Chemical Plant Maintenance has emerged as an indispensable tool for professionals in this field, offering precision, efficiency, and safety in flange surface treatment.
The Importance of Flange Preparation in Chemical Plants
Flanges serve as the critical connection points in chemical processing systems, joining pipes, valves, pumps, and other equipment. Proper flange preparation is essential because:
- It ensures leak-proof connections in systems handling hazardous chemicals
- Maintains system integrity under high pressure and temperature conditions
- Prevents contamination of chemical processes
- Extends the service life of gaskets and sealing components
- Reduces downtime during maintenance operations
Traditional methods of flange preparation, such as manual grinding or filing, often prove inadequate for the stringent requirements of chemical plant maintenance. This is where specialized flange preparation machines make a significant difference.
Features of Modern Flange Preparation Machines
Contemporary flange preparation machines designed for chemical plant maintenance incorporate several advanced features:
1. Precision Machining Capabilities
These machines offer micron-level precision in surface finishing, ensuring perfect flatness and surface texture for optimal gasket seating. Advanced models can achieve surface finishes as smooth as 0.8 μm Ra, far superior to manual methods.
2. Versatility in Flange Types
Modern machines can handle various flange types commonly found in chemical plants, including:
- Weld neck flanges
- Slip-on flanges
- Lap joint flanges
- Socket weld flanges
- Blind flanges
3. Corrosion-Resistant Construction
Given the corrosive environments in chemical plants, these machines are built with stainless steel components and protective coatings to withstand exposure to chemicals and prevent contamination of flange surfaces.
4. Portable Design
Many models are designed for portability, allowing technicians to bring the machine directly to the flange location rather than removing the flange for off-site machining. This significantly reduces downtime during maintenance operations.
5. Automated Operation
Advanced models feature programmable controls that automate the machining process, ensuring consistent results and reducing operator fatigue. Some systems include digital displays for precise control of cutting parameters.
Benefits of Using Flange Preparation Machines
The adoption of specialized flange preparation equipment in chemical plant maintenance offers numerous advantages:
Enhanced Safety
By eliminating the need for manual grinding or cutting, these machines reduce the risk of operator injury and minimize spark generation in potentially explosive environments.
Improved Efficiency
A typical flange preparation machine can complete surface treatment in minutes compared to hours required for manual methods. This dramatically reduces maintenance downtime and associated production losses.
Consistent Quality
Automated machines deliver uniform results across all flange preparations, eliminating human error and ensuring reliable sealing performance throughout the plant.
Cost Savings
While the initial investment may be significant, the long-term savings from reduced