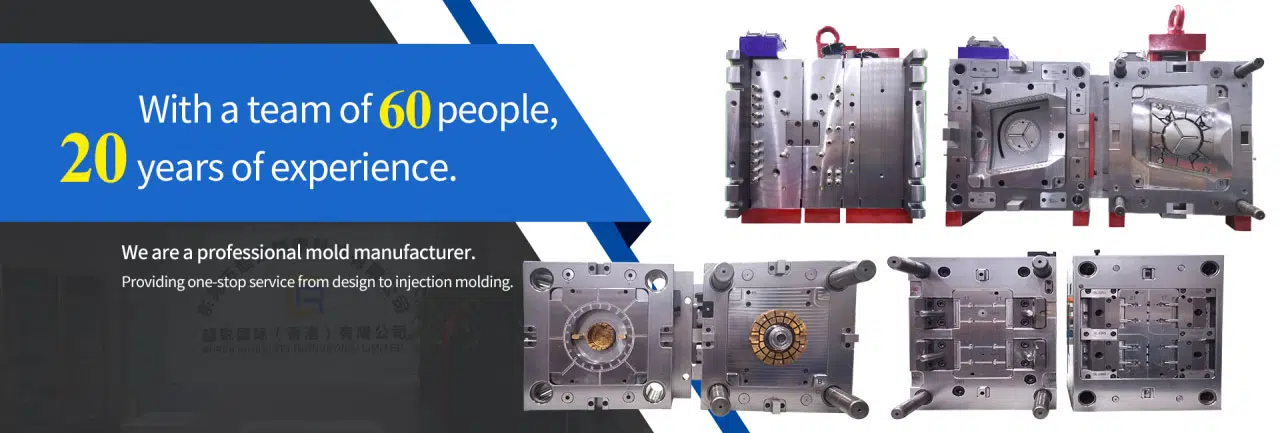
,文章长度在1000字左右。html
Tooling Innovations in Industrial Design
Industrial design has always been at the forefront of innovation, shaping the way products are conceived, developed, and manufactured. One of the most critical aspects of this process is tooling—the specialized equipment and techniques used to create molds, dies, and other components essential for mass production. Over the years, advancements in tooling have revolutionized industrial design, enabling greater precision, efficiency, and creativity.
The Evolution of Tooling in Industrial Design
Tooling has come a long way from its early days of manual craftsmanship. In the past, molds and dies were painstakingly carved by hand, limiting both the complexity and scalability of designs. The advent of Computer Numerical Control (CNC) machining in the mid-20th century marked a turning point, allowing for automated, high-precision manufacturing. Today, technologies like 3D printing and laser cutting have further expanded the possibilities, making it easier than ever to produce intricate and customized tooling components.
Key Innovations in Modern Tooling
Several groundbreaking innovations have emerged in recent years, each contributing to the advancement of industrial design:
1. Additive Manufacturing (3D Printing)
Additive manufacturing has transformed tooling by enabling the creation of complex geometries that were previously impossible or prohibitively expensive. Designers can now prototype and produce tools with internal channels, lightweight structures, and customized features, all while reducing material waste. This technology has also shortened lead times, allowing for faster iterations and more agile development cycles.
2. Smart Tooling with IoT Integration
The Internet of Things (IoT) has brought intelligence to tooling systems. Sensors embedded in molds and dies can monitor temperature, pressure, and wear in real time, providing valuable data to optimize production processes. Predictive maintenance algorithms can alert operators to potential issues before they cause downtime, improving overall efficiency and reducing costs.
3. Advanced Materials
The development of high-performance materials, such as carbon fiber composites and ultra-durable polymers, has expanded the capabilities of tooling. These materials offer superior strength, heat resistance, and longevity, making them ideal for demanding industrial applications. Additionally, they often reduce the weight of tools, improving handling and energy efficiency.
The Impact of Tooling Innovations on Industrial Design
These advancements have had a profound impact on the field of industrial design. Designers now have unprecedented freedom to experiment with forms and functions, knowing that tooling technologies can bring even the most ambitious concepts to life. Moreover, the ability to produce smaller batches cost-effectively has opened doors for niche markets and customized products, fostering innovation across industries.
From automotive to consumer electronics, tooling innovations are driving progress in every sector. As these technologies continue to evolve, the boundaries of what’s possible in industrial design will keep expanding, paving the way for a future where creativity and precision go hand in hand.
Looking Ahead: The Future of Tooling
Keyword: Tooling & Industrial Design
The future of tooling in industrial design is bright, with emerging technologies like artificial intelligence (AI) and nanotechnology poised to take center stage. AI-powered design tools could automate the creation of optimized tooling components, while nanomaterials might enable self-healing molds that extend their own lifespan. As these innovations mature, they will further blur the line between design and manufacturing, creating a seamless workflow from concept to production.
Ultimately, the continued evolution of tooling will empower industrial designers to push boundaries, create sustainable solutions, and deliver products that meet the ever-changing needs of consumers and industries alike.