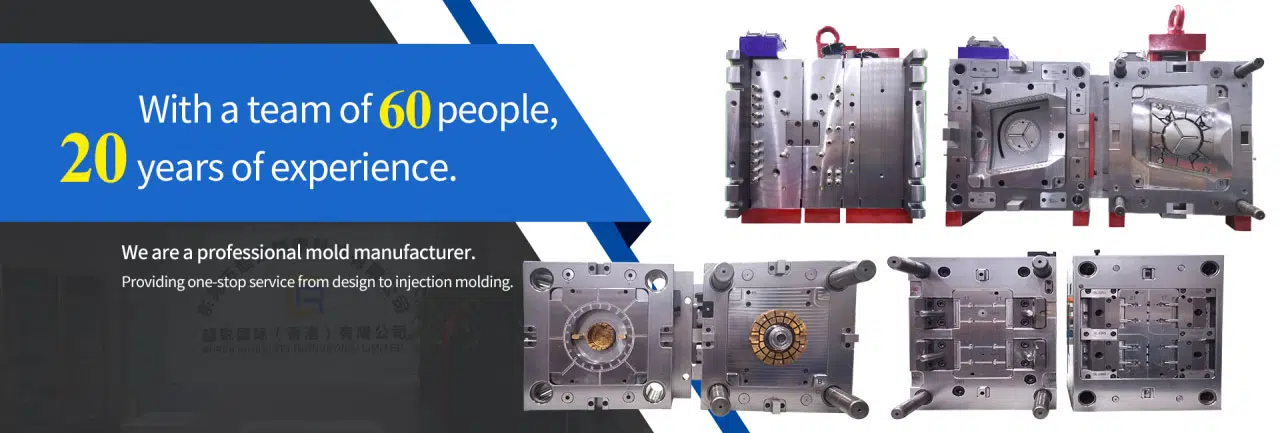
# Vacuum Casting Technology in Modern Manufacturing
## Introduction to Vacuum Casting
Vacuum casting is a versatile manufacturing process that has gained significant popularity in modern production environments. This technique combines the precision of traditional casting methods with the efficiency of vacuum-assisted molding to create high-quality parts with excellent surface finishes.
## How Vacuum Casting Works
The vacuum casting process involves several key steps:
– Creating a master pattern (typically using CNC machining or 3D printing)
– Making a silicone mold from the master pattern
– Placing the mold in a vacuum chamber
– Pouring liquid material (usually polyurethane resin) into the mold
– Allowing the material to cure under vacuum conditions
– Removing the finished part from the mold
## Advantages of Vacuum Casting Technology
Vacuum casting offers numerous benefits that make it attractive for modern manufacturing:
– Cost-effective for small to medium production runs
– Excellent dimensional accuracy and surface finish
– Ability to replicate complex geometries
– Wide range of material options with varying properties
– Faster turnaround times compared to traditional tooling methods
– Suitable for prototyping and low-volume production
## Applications in Various Industries
Vacuum casting technology finds applications across multiple sectors:
### Automotive Industry
Used for creating functional prototypes, interior components, and under-the-hood parts that require heat resistance.
### Medical Devices
Ideal for producing surgical instruments, device housings, and other medical components that demand precision and biocompatibility.
### Consumer Electronics
Employed in manufacturing casings, buttons, and other plastic components with tight tolerances.
### Aerospace
Used for lightweight components that require specific material properties and dimensional stability.
## Material Options in Vacuum Casting
Modern vacuum casting systems support a wide variety of materials:
– Standard polyurethane resins
– Flexible and rubber-like materials
– High-temperature resistant resins
– Transparent and translucent materials
Keyword: Vacuum Casting
– Flame-retardant compounds
– FDA-compliant materials for food contact
## Future Trends in Vacuum Casting Technology
The vacuum casting industry continues to evolve with several emerging trends:
– Development of new resin formulations with enhanced properties
– Integration with digital manufacturing workflows
– Improved automation in mold preparation and part removal
– Expansion of material options to include bio-based resins
– Enhanced quality control through in-process monitoring
## Conclusion
Vacuum casting technology has established itself as a valuable tool in modern manufacturing, bridging the gap between prototyping and mass production. Its ability to produce high-quality parts quickly and cost-effectively makes it particularly valuable in today’s fast-paced product development cycles. As materials and processes continue to improve, vacuum casting will likely play an even greater role in manufacturing across diverse industries.