Tape Manufacturing: Processes, Materials, and Applications
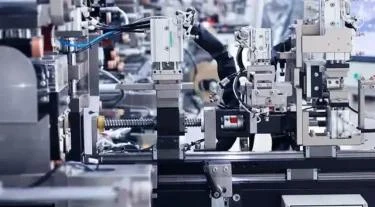
# Tape Manufacturing: Processes, Materials, and Applications
## Introduction to Tape Manufacturing
Tape manufacturing is a complex process that involves various materials and techniques to produce adhesive products for countless applications. From everyday household uses to industrial applications, tapes play a crucial role in modern life. The manufacturing process has evolved significantly over the years, incorporating advanced technologies to meet diverse requirements.
## The Tape Manufacturing Process
### 1. Material Preparation
The first step in tape manufacturing involves preparing the base materials. This includes:
– Selecting the appropriate backing material (paper, plastic, cloth, or foil)
– Preparing adhesive compounds
– Gathering release liners and other necessary components
### 2. Coating Process
The coating process is where the adhesive is applied to the backing material. There are several coating methods:
– Hot melt coating
– Solvent-based coating
– Water-based coating
– UV-cured coating
Each method has its advantages and is chosen based on the desired tape characteristics.
### 3. Drying and Curing
After coating, the tape goes through drying or curing processes:
– For solvent-based adhesives: evaporation drying
– For water-based adhesives: infrared or hot air drying
– For UV-cured adhesives: exposure to ultraviolet light
### 4. Slitting and Rewinding
The final manufacturing steps include:
– Precision slitting to desired widths
– Rewinding onto cores
– Packaging for distribution
## Common Materials Used in Tape Production
### Backing Materials
– Polypropylene (PP)
– Polyethylene (PE)
– Polyvinyl chloride (PVC)
– Paper
– Cloth
– Metal foils
### Adhesive Types
– Acrylic
– Rubber-based
– Silicone
– Hot melt
– Pressure-sensitive
### Special Additives
– UV stabilizers
– Flame retardants
– Conductive materials
– Reinforcing fibers
## Applications of Manufactured Tapes
### Industrial Applications
– Electrical insulation
– Automotive assembly
– Aerospace components
– Construction sealing
### Consumer Applications
– Packaging
– Stationery
– Home repair
– Arts and crafts
### Medical Applications
– Surgical tapes
– Wound care
– Diagnostic devices
– Prosthetic attachments
## Quality Control in Tape Manufacturing
Manufacturers implement rigorous quality control measures including:
– Adhesion testing
– Tensile strength measurements
– Temperature resistance checks
– Aging tests
– Consistency evaluations
## Future Trends in Tape Manufacturing
The tape manufacturing industry continues to evolve with:
– Development of eco-friendly materials
– Smart tapes with embedded technology
– Improved performance under extreme conditions
– Customizable adhesive properties
– Automated production systems
## Conclusion
Tape manufacturing is a sophisticated process that combines material science with precision engineering. As technology advances, we can expect to see even more innovative tape products serving an expanding range of applications across industries. The future of tape manufacturing promises smarter, stronger, and more sustainable solutions to meet the world’s bonding and sealing needs.
Keyword: tape manufacturing